Tesla Teases Manufacturing Process That Could Cut Costs Drastically For New $25,000 BEV
Summary:
- The automaker’s newest plant near Monterrey, Mexico, reportedly will ditch a moving assembly line that has been industry mainstay for more than a century.
- Tesla remains vague on details and hasn’t yet tested system that relies on fewer parts and use of the battery as integral to a vehicle’s structure.
- Should Tesla’s vehicle assembly system prove viable, battery-electric rivals could face competitive pressure to revise operations.
- Improved prospects for profitable low-cost BEV model strengthens Tesla’s investment case.
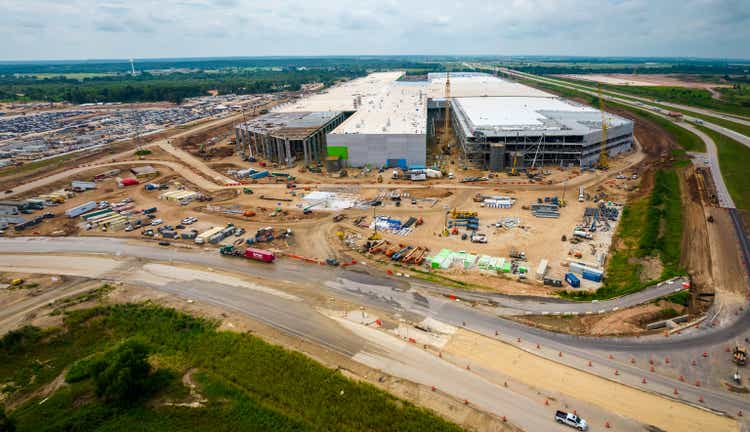
The now-completed Tesla Gigafactory Austin, known as GigaTexas, shows construction progress and the 4680 battery factory.
RoschetzkyIstockPhoto/iStock Editorial via Getty Images
More than a century ago, Henry Ford revolutionized personal transportation with the development of the moving assembly line, whose cost efficiency helped bring automobiles within reach of the average American consumer. A global industry was born.
Elon Musk is proposing a groundbreaking innovation for the manufacture of battery-electric vehicles that – if proven valid – could bring low-cost Tesla models to consumers who now couldn’t afford or aren’t prepared to pay for the company’s Model 3, its lowest price model, which starts at about $45,000.
In early March, at Tesla’s (NASDAQ:TSLA) investor day, Lars Moravy, vice president of vehicle engineering, described for journalists and analysts how the automaker intends to reduce manufacturing costs by 50%, expanding on a system developed for the Model Y that replaces the moving assembly line by building the vehicle in five separate large segments that are knitted together at the end of the assembly process.
Parts reduction
The front, rear, left side, right side and floor of the vehicle are built separately. The floor consists mainly of the battery, which functions as a structural component as well as the power source.
Large aluminum castings in the new low-cost Tesla model replace many steel castings used for most vehicles today that must be welded together. The five modules would be joined together – perhaps with glue and other fasteners, according to one guess – and a glass roof is added.
Several advantages would accrue from modular manufacture over the assembly line method – at least in theory. When a problem arises on an assembly line, the entire line must shut down while it is fixed. In a modular system, a snafu in one area won’t hurt efficiency in other modules.
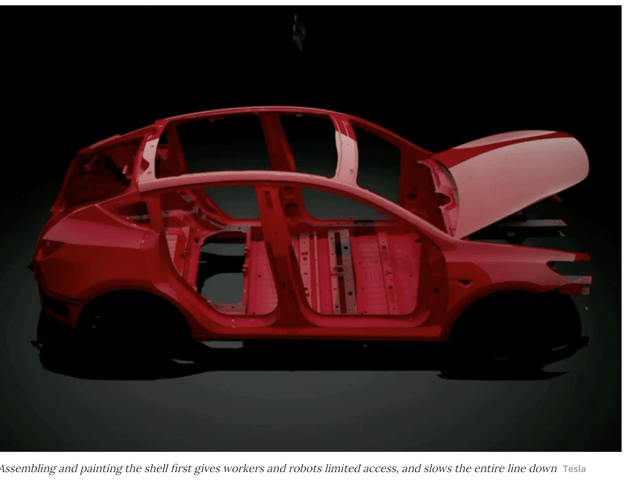
Conventional body assembly (Tesla)
On today’s automotive assembly line, a “body in white” or completed cabin moves from station to station, where workers or robots install seats, windows, instrument panels and so forth.
Under Tesla’s proposed systems, two half bodies (left and right) are assembled in modules, complete with interior components. Large aluminum castings – “gigacastings” – constitute front and rear modules, with relevant mechanical and electrical components added. Tesla’s battery takes on a structural role, its casing serving as the floor.
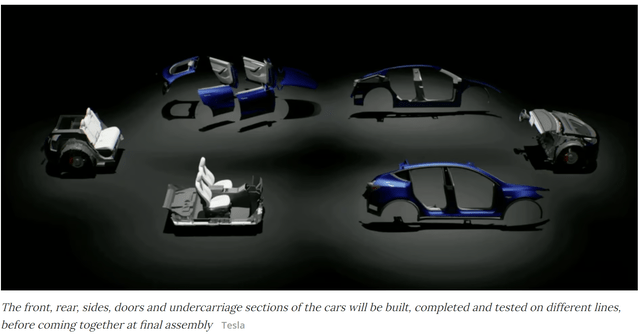
Tesla modular assembly (Tesla)
All five large components are joined together with fasteners and, perhaps, glue – topped by the glass roof. In theory, labor is drastically reduced as well as much awkwardness needed to install components into an already enclosed body in white.
Outmoded Process?
Can Tesla’s proposed overthrow of the century-old moving assembly actually work? No one knows until Tesla manufacturing engineers prove it. Some may remember Musk promising back in 2016 that he intended to revolutionize automotive manufacturing, not just the car’s propulsion system to battery from internal combustion. “Machines building machines” is the way he put it – to much laughter by old hands in the car business.
John McElroy, president of Blue Sky Productions, who has covered automotive engineering since the 1980s said:
“To me, if Tesla can pull off this new way to make cars, it’s going to be the most significant change in automotive assembly since those guys at Ford tied a rope on the chassis of a Model T and started winching it across the floor 120 years ago.”
I also phoned some contacts at Toyota, which is known for its manufacturing prowess. They said they found Tesla’s new manufacturing concept “quite interesting” and a development worth watching.
As Musk and Tesla discovered, building vehicles at scale turned out to be a whole lot trickier and less susceptible to a quick and simple revolution than he imagined. Which is why he once described himself as trapped in “manufacturing hell,” spending nights at Tesla’s west coast assembly plant in a sleeping bag.
New Wave
Yet Musk’s grit and innovative mindset, his proclivity for a ground-up first principles rethink, now are legend. One only has to observe how Space-X booster rockets now return and land themselves on launch pads after launching their payloads – after so many decades of watching booster rockets fall into the sea as junk – to be reminded how Musk’s creativity can overturn convention.
Moravy at the March Investor Day described the advantages of what Tesla calls “Parallel Manufacturing” this way:
“In the end, what does that mean? To increase the scale of electric vehicles (by) orders of magnitude, we have to make the constraints part of the solution. It leads us to more than 40% reduction in footprint, which means we can build factories faster, with less capex and more output per unit dollar. It also means that, through this innovation and some of what my other engineering colleagues will talk to you about in the future, we’ll reduce costs as much as 50%. This is the 2-for-1 concept you hear me and Elon talking about on earnings calls.”
For a thorough explanation of Tesla’s “Parallel Manufacturing” from the March briefing, check out this video.
From an investment standpoint, I can’t see much risk in what Tesla is attempting. Parallel manufacturing will work – or not. If not, many in the auto industry will have a good chuckle, and Tesla engineers will return to the current assembly-line system and figure out other ways of improving efficiency and lowering cost.
If, however, the new assembly methods prove viable and reduce costs as projected, a sea change will overtake the auto industry. For Tesla shareholders, the first-mover benefits could be immense. Tesla vehicles already have evolved into status symbols for the wealthy – and they soon could be affordable as status symbols for middle class buyers as well, which would bring a big bounty to the company’s bottom line.
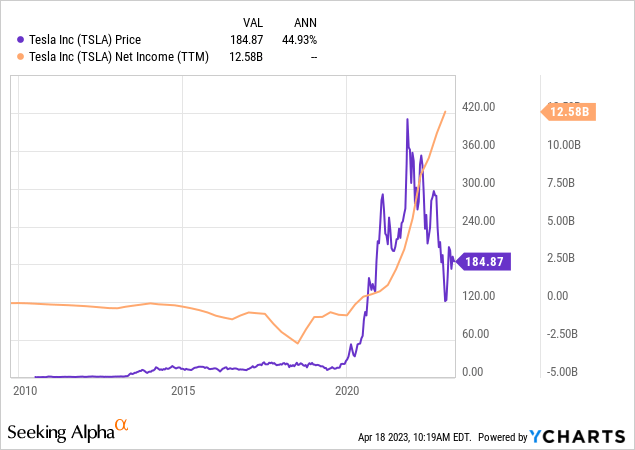
Over the past 12 years I have evolved from a Tesla skeptic into a cautious believer based on the company’s continued growth in vehicle sales, revenue and earnings – not to mention the cachet of the product.
In addition to its fifth assembly plant in Mexico, Tesla currently has capacity to build about 2 million cars a year at four factories, in Fremont, California, Shanghai, China, Austin, Texas, and Berlin, Germany. It has set a goal of eventually building 20 million cars a year. The company delivered just over 1.3 million cars in 2022. The largest automaker in the world by production volume, Toyota, delivered just over 10 million cars globally in 2022.
If you are a Tesla shareholder, pay close attention to the evolution of the new Mexico plant – and its assembly operations. If you’re a skeptic or a short seller, you may wish to adjust the needle from sell to hold.
Analyst’s Disclosure: I/we have a beneficial long position in the shares of TSLA either through stock ownership, options, or other derivatives. I wrote this article myself, and it expresses my own opinions. I am not receiving compensation for it (other than from Seeking Alpha). I have no business relationship with any company whose stock is mentioned in this article.
Seeking Alpha’s Disclosure: Past performance is no guarantee of future results. No recommendation or advice is being given as to whether any investment is suitable for a particular investor. Any views or opinions expressed above may not reflect those of Seeking Alpha as a whole. Seeking Alpha is not a licensed securities dealer, broker or US investment adviser or investment bank. Our analysts are third party authors that include both professional investors and individual investors who may not be licensed or certified by any institute or regulatory body.